1898年,大连船舶重工集团(以下简称大船集团)的前身——中东铁路公司造船工场建立,并从一个不起眼的“小坞”发展到现在成为造船业的强者,从顺利交付中国第一艘航空母舰“辽宁舰”到首艘国产航母成功下水再到首艘20000TEU集装箱船成功交付,一个个傲娇佳绩的背后,是靠不间断的创新精神使这座百年集团经久不衰。
1 项目背景
1.1 项目改进前情况
为提高船舶经济性,目前在艉轴位置增设节能导轮已成为一种较为常规的设计方式,由于节能导轮线型变化较大、内部空间狭小、加强数量较多,加强与外板对应位置确定困难,目前通过在导轮外板处手工开设塞焊孔进行焊接。
1.2 项目改进前存在的问题
(1)手工开设塞焊孔费时费力;
(2)塞焊孔数量较多,手工开工效率低下,极大地延长了建造周期
(3)手工开设的塞焊孔工艺美观性差
2 应用TRIZ理论到节能导轮塞焊孔的过程
2.1 目前的工艺流程:
工序之间的功能作用关系:
根据工序的完成水平情况,提出两个解决方案:
方案1:随着大船集团建造经验的不断积累,建造精度随之不断提高,设计人员可在钢板展开图上对塞焊孔进行准确定位,以此为基础,对塞焊孔工艺流程进行再造。将开孔工序向前一道工序转移,由设计人员提供设计数据和切割程序,利用数控切割机预先开孔,然后完成钢板的冷弯加工,具体流程如下:
方案2:裁减掉开设塞焊孔的工序,通过优化节点的形式,取消导轮外板塞焊孔,从根本上简化工艺流程。
2.2 因果链分析
根据因果链分析,提出两个解决方案:
(1)提供适宜的生产场地,在导轮装配前用自动切割设备加工;
(2)优化施工工艺,降低塞焊孔数量,甚至取消塞焊孔。
2.3 技术矛盾
在进行过程功能分析中,提出了将开孔迁移至钢板冷弯工序前,在进行这种工序前移时,出现了一堆技术矛盾。若保持目前的工序流程,将会降低分段部的生产效率,但会提高钢加公司钢板冷弯的可靠性;若是进行工序迁移,将会提高分段部的生产效率,但会降低钢加公司钢板冷弯的可靠性。
(1)确定要解决的技术矛盾为EC-1,它发生在(生产效率)与(可靠性)之间,发生在(工序调整)的时候。
(2)模型问题——对应的39个通用工程参数
改善的参数:27可靠性
恶化的参数:39生产效率
(3)解决方案模型,对应查看阿奇舒勒矛盾矩阵表得到参考创新原理为:1为分割原理、35改变物理或化学参数、10预先作用原理、38强氧化剂原理。
根据创新原理提出2个技术方案:
(1)应用创新原理1分割原理,将需要开设的塞焊孔的位置设置为板缝,通过板缝的焊接实现外板与结构之间的连接。
(2)应用创新原理10预先作用原理,通过设计三维数据,预先将结构与外板之间的对位位置在数控划线中体现,并应用切割程序确保切割位置与理论位置一致。
3 技术方案整理与评价
通过应用TRIZ工具,获得了如下技术方案:
方案1:将开孔工序向前道工序前移,由设计人员提供设计数据和切割程序,利用数据切割机预先开孔,后完成钢板的冷弯加工。
方案2:裁减掉开设塞焊孔的工序,通过优化节点形式,取消导轮外板塞焊孔,从根本上简化工艺流程。
方案3:提供适宜的生产场地,在导轮装配前利用自动切割设备加工。
方案4:优化施工工艺,降低塞焊孔数量,甚至取消塞焊孔。
方案5:将需要开设塞焊孔的位置设置为板缝,通过板缝的焊接实现外板与结构之间的连接。
方案6:通过设计三维数据,预先将结构与外板之间的对位位置在数控划线中体现,并应用切割程序确保切割位置与理论位置一致。
通过对以上方案的整理与考量,主要得出两个综合型解决方案:
1. 由设计院提供基础数据和切割程序,在导轮外板切割阶段完成塞焊孔的切割工作,然后进行外板的冷弯加工,避免分段阶段的开孔工作。
2. 修改导轮内部结构与外板的节点形式,将原本的“T”字节点优化为“十”字结构,充分利用外板的板厚,完成外板与结构的连接。
4 项目改进实施情况
为验证此种工序的可行性,大船集团对该项目进行了开孔冷弯试验,现场效果良好,钢板探伤亦未发现缺陷,后续将在T308K船上进行先划线后冷弯的试验,对塞焊孔位置冷弯后位置变化进行测量跟踪,若符合生产需求,将在实船上进行应用。
责编/李曼
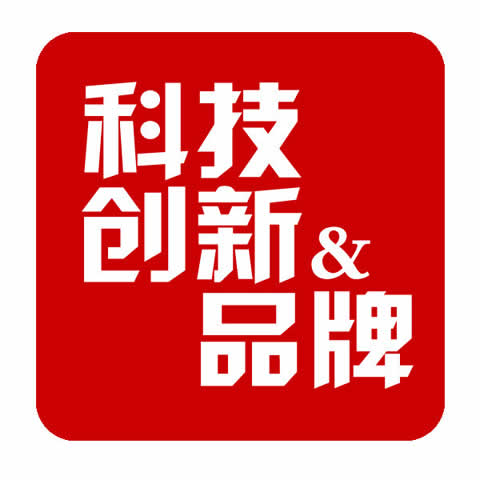