1 绪论
船舶的精度管理水平是反映船舶建造企业水平的重要指标之一,是关系到船舶制造智能化和数字化能否实现的关键。自主管理是精度管理的重要组成部分,同时全面的自主管理也是精度管理的目标和方向。大连船舶重工集团近年来高度重视精度自主管理工作,主要的生产工序均已形成了良好的自主管理体系,基本形成了精度控制点“有点必检,有检必留痕”的精度管理理念和施工习惯。但是平整度的自检率与其他精度控制点相比差距较大,针对该问题,我们使用创新理论TRIZ方法进行了分析和解决。
2 当前问题描述
未使用TRIZ方法创新之前,大船集团生产现场的平整度检测状况如下所示:当测量一个构件的平整度时,需要两个人拉拽粉线的两端,另一个人使用钢直尺测量粉线与钢板尺之间的间隙。该检测方式不仅检测效率低,而且检测精度极差,因此导致施工人员工作积极性较差,平整度的自检率提升幅度极慢。
图1 粉线+钢直尺的检测方式
3 运用TRIZ系统分析工具对系统进行分析
3.1功能分析法的应用
首先使用功能分析法,对当前的检测系统进行了分析。
通过功能分析法,发现当前系统存在五个问题:其一是粉线需要人移动和拉紧绷直;其二是钢板尺需要人移动和读数;其三是钢板尺刻度依赖构架与粉线的限制;其四是粉线需要贴合构件,否则影响精度;其五是钢板尺与构件贴合易产生磨损。
图2 功能分析图
3.2因果链分析法的应用
通过因果链分析法,确定了要解决的关键问题和根问题,后续TRIZ工具的使用正是为了解决这些根问题。随后又使用了资源分析法,最终理想解分析法等,找到了产品的最终目标和可以利用的资源。
针对因果链分析法中产生的小问题,通过功能裁剪法,确定了最终功能模型,仅仅需要一个人即可进行检测。
4 基于发明原理的舰船平整度检测方式设计
4.1技术矛盾描述
通过上述分析法,得到两大技术矛盾:其一是“检测组件与构件接触滑动”和“工具磨损”之间的矛盾;其二是“多种测量要求”和“便于携带和测量”之间的矛盾。
图3 因果链分析法
4.2问题概念解决方案
在第一组技术矛盾中,问题模型分别对应39个通用工程参数,需要改善的参数为:(25)时间损失、(10)力;恶化的参数为:(33)物质损失。根据上述矛盾查找阿奇舒勒矛盾矩阵表,找到推荐的解决原理是:14号(曲面化原理)、15号(动态性)、18号(机械振动)、40号(复合材料)、35号(物理或化学参数变化)、10号(预先作用原理)、27号(廉价替代原理)7个推荐原理。通过上述推荐原理的仔细分析,发现对解决第一个矛盾有设计指导的发明原理如下。
第14号原理(曲面化原理) :将接触位置由滑动摩擦改为滚动摩擦。
第40号原理(复合材料):使用耐磨的构件与钢板接触。
第10号原理(预先作用原理):摩擦部位提前涂抹润滑油。
第27号原理(廉价替代原理):接触部位使用廉价的构件,磨损影响影响精度后,对其进行替换。
在第二组技术矛盾中,问题模型分别对应39个通用工程参数,需要改善的参数为:(35)适用性;恶化的参数为:(4)静止物体的长度、(37)控制测量的复杂性。根据上述矛盾查找阿奇舒勒矛盾矩阵表,找到推荐的解决原理是: 15号(动态性)、34号(抛弃和再生)、1号(分割)、27号(廉价替代原理)、7号(嵌套) 5个推荐原理。通过上述推荐原理的仔细分析,发现对解决第一个矛盾有设计指导的发明原理如下。
第15号原理(动态性) :将测量滑动部分做成可拆卸,根据测量要求安装到不同尺寸横梁上以满足测量要求。
第1号原理(分割):将组件(横梁部分)分割成可组装的不同部分,根据长度需求组装。
第7号原理(嵌套):将横梁做成伸缩的构件,根据检测要求调整长短。
4.3物理矛盾解决方案
在4.2中提到的两组技术矛盾中,均存在物理矛盾。在第一组矛盾中,出现的物理矛盾如下:横梁应该(长),以满足(测量范围)要求;但是,横梁应该(短),以满足(便于携带)要求;在第二组矛盾中,出现的物理矛盾如下:测量点应该(多),以满足(检测精度)要求;但是,测量点应该(少),以满足(提高效率)要求。
针对第一组物理矛盾,解决方案如下。
(1)时间分离法:工装横梁设计为折叠形式,使用时展开,不使用时折叠。
(2)整体与局部分离法:测量组件和横梁分开,便于携带的同时根据测量需求选择横梁。
(3)空间分离法:分割成各个可以连接的小段,根据使用需求连接。
针对第二组物理矛盾,解决方案如下。
(4)时间分离法: 减少每个点测量时读数时间(减少有害作用时间原理);测量设备在滑动过程中一直保持测量模式,不间断测量(有益作用连续性)。
(5)整体与局部分离法:只选择测量偏差最大的点,从而掌握整体平整度状态。
4.4 概念解决方案
通过方案的论证和选择,最终选择了如下可能的概念方案。
图4 新的检测工具
(1)方向性方案上,选择制作一种廉价的接触性检测工装;
(2)组件模型方案上,选择钢板尺在横梁上组合并滑动;
(3)解决钢板尺磨损问题上,选择接触部位由滑动摩擦改为滚动摩擦;
(4)在便于携带问题上,选择将横梁制作为一种可伸缩的嵌套结构;
(5)在解决测量点过多问题上,选择让滑动组件在滑动过程中保持持续的测量;
(6)在解决检测后自动标记留痕问题上,选择了滑动组件滑轮处增加一个涂色功能,检测后在构件上留下痕迹;
(7)读数困难上,除了增加一个显示屏幕外,还增加了声音提示组件,使其可以超差语音提醒。
通过详细方案的选取,设计制作了新的检测工具如图4所示。
图5 塞尺+直横梁的检测方式方式 图6 气泡水平尺的检测方式 图7 扫描设备的检测
5 成果分析与效益
行业内外传统的平整度检测方式除了船舶企业采用的粉线+钢直尺的检测方式外,还有塞尺+直横梁、气泡水平尺、扫描设备三种检测方式,但均存在不同程度的不足,具体表现为:
(1) 塞尺+直横梁 :检测效率低,依赖人工读数(见图5);
(2)气泡水平尺:不具备读数功能,无法智能检测平整度的优劣(见图6);
(3)扫描设备:价格昂贵,无法在船企大规模推广(见图7)。
该创新项目从现场的实际难题出发,解决工厂生产过程中急需解决的难题,具备高效率高精度低成本的特点。其亮点在于四个方面:一是具备电子显示读数功能,超差声音提示功能,提升读数的精度及检测效率;二是检测工具各部位间均为可拆卸的滑轮连接,适应多种检测要求,各部件损坏可进行更换;三是横梁采用可伸缩的嵌套结构,便于携带;四是检测组件通过滑轮在检测对象上滑动,一次可测量一条线上的全部测量点,提升检测效率4倍以上。
图8 原方案与创新方案对比示意图
通过新检测方式的推广使用,在检测效率上由原来的测量一个点需要9秒,到现在的测量一条线仅仅需要4秒,检测效率提高了4倍以上;在检测精度上,由原来人工读数的平均偏差0.5mm提升到了电子屏幕显示读数的0.1mm,检测精度提高了5倍。
工欲善其事,必先利其器。随着检测工具在检测效率,检测精度和便携性上的提升,施工人员对平整度的自检率也由原来的46.7%提升到了91.4%。平整度水平的提升,不仅大幅度提升建造质量,还大大减少了分段、总组合拢工序对平整度的修正人工工时和材料浪费,每年带来的经济效益在110万元以上。该项目已经制作出了新的检测工具,并已经投入使用中,其廉价,高效,高精度的特点广泛适用于工程领域,在平整度的检测方面具备较高的推广价值和市场空间,在后续可能承接的超大型集装箱船止裂钢精度控制、薄膜型LNG船平整度控制上具备更好的应用前景。该项目已经申请了国家专利,并获得了辽宁省创新大赛金奖。
责编/李雪敏
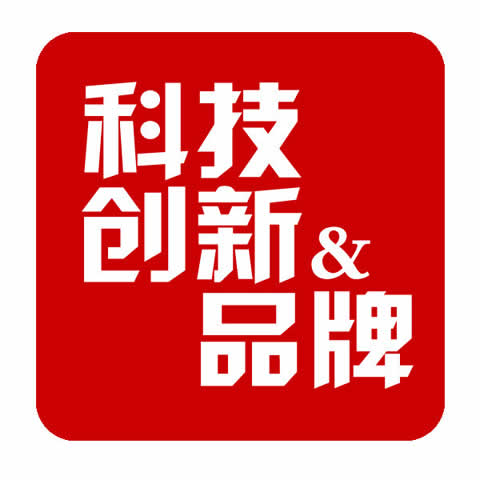