我国的塑料制品行业近些年不断发展,消费量及产量都位居全球首位,出口增速加快。在塑料制品行业中,国内主要以中低档产品为主,整个制品行业缺乏高端技术,只有不断提高塑料制品的品质与用途,向高端市场进军,才能为塑料制品的发展带来更多机遇。石唯光先生任职于大型国有石化企业和世界500强石化公司,于2010年创立上海聚凯实业有限公司,带领公司技术团队致力于改性塑料、工程塑料、新型3D打印材料等高分子化工产品的研发和技术创新,取得了多项专利技术。其产品已经广泛应用于汽车、航空航天、建材、医疗器械以及先进制造等领域。部分产品拥有较高的市场份额,为推动中国化工行业的科技创新和发展做出了卓越的贡献。石唯光先生在百忙之中接受了笔者的专访,让我们一起去探访他的塑料工业王国。
笔者:您多年从事塑料等高分子材料的研发,以您在业内的经历,能否介绍一下中国塑料行业的现状?
石唯光:好的。现在可以这样讲:塑料已经与钢铁、木材、水泥一起构成现代社会中的四大基础材料,是支撑现代高科技发展的重要材料之一,是信息、能源、工业、农业、交通运输乃至航空航天和海洋开发等国民经济各重要领域都不可缺少的生产资料,是人类生存和发展离不开的消费资料。随着科技的告诉发展和人民生活水平的提升,很多传统工业都在发生着变革,其中,化工塑料制造业凭借其产品成本低廉与品种繁多的优势,成为了行业发展的佼佼者。近年来,我国的塑料制品业快速发展,其增长速度远远高于世界塑料行业的平均增长速度,我国塑料产量从 2007 年的3,305.23 万吨增长到 2014 年的 7,387.78 万吨,塑料制品消费量、产量居世界首位。
笔者:中国塑料制品行业的发展水平与发达国家相比又如何呢?
石唯光:还是有一定的差距,现在中国塑料制品行业主要以中低档产品为主,整个制品行业缺乏高端技术。作为衡量一个国家塑料工业发展水平的塑钢比指标,我国仅为30:70。世界平均塑钢比指标是50:50,发达国家如美国达到70:30,德国达到63:37。我们国家的塑钢比指标远远达不到这些水平,人均塑料消费量与世界发达国家相比还有很大的差距。未来随着我国改性塑料的技术发展和消费升级,塑料制品预计可保持10%以上的增速,庞大的下游行业为我国塑料制品行业的发展提供了强有力的支撑。
笔者:汽车用塑料合金和高分子材料就是塑料制品的下游行业之一。汽车工业对于以塑代钢的需求逐渐增加。您在这方面有哪些技术成果?
石唯光:汽车工业是发达国家工程塑料应用最为广泛、使用量最大的工业门类,也是中国工程塑料最有发展潜力的领域之一。随着汽车轻量化的发展,塑料在汽车中的比例越来越高。一部车下来,汽车塑料总用量可占汽车自重的5%-10%。汽车的内饰、外饰、发动机周边、HVAC系统以及照明系统所用的材料中都离不开工程塑料。因此,我带领公司研发团队研制了多种汽车用PC/ABS、ABS塑料合金制品。比如高电镀结合力塑料合金可以解决橡胶在树脂中分散的问题,确保材料电镀时的高结合力,改善了镀层起皮、起泡,甚至在使用过程中剥落的情况。新车内的气味一直是消费者关注的问题,我们研发的低污染的内饰用塑料合金可以从源头上有效减少汽车内饰件带来的车内空气污染。还有可以直接利用的美学内饰材料,为汽车内饰的美化提供了更多创意。
笔者:海军舰艇、航天科技、医学、电子等需要高端的定制化产品的领域中,工程塑料也有广泛应用,3D打印就是一种应用方式,其材料质量直接影响着打印成品的质量。您研发出的新型3D打印用材料有哪些优势?
石唯光:普通的3D打印线材通过熔融堆积技术制造的打印件表面不够光洁,常有层状痕迹,这制约了3D打印技术的发展,我们创新的高光洁度3D打印材料就能解决这个问题,得到的打印制品可以媲美于注塑件的效果。另外,目前3D打印常用的普通PLA材料在韧性和力学性能上跟很多工程塑料相比有较大不足,我们改进后的高韧性PLA把普通PLA的韧性提高了近10倍,整体力学性能比ABS要高10%以上。这些技术创新大大拓展了3D打印技术的应用空间。
笔者:您在塑料工业方面的重要贡献和突出成绩为自己赢得了很多荣誉,获得了不少奖项。让您印象最深刻的奖项是什么?
石唯光:从业这么多年,确实也取得了不少成绩,获得了不少奖项。对我而言意义重大的奖项主要有两个,一个是中国化工行业科技成果创新奖一等奖,另一个是2014中国塑料工业年度科技人物奖,这两个奖项都与“科技创新”分不开。科技创新是获得所有成绩的最重要的因素,我们为此投入了大量人力物力财力,能够凭借“科技创新”获奖,我是非常高兴的。国际上发达国家的塑料工业领先我们很多,想要缩小差距只能自己埋头苦干,碰到弯路、遇到困难都是最正常不过的事情。正是有了前期的经验和教训,才换来我们今天的成绩和荣誉。路漫漫其修远兮,吾将上下而求索。创新这条路上,前方充满了未知,但我们仍会坚持走下去,给中国的塑料工业带来更多的贡献。
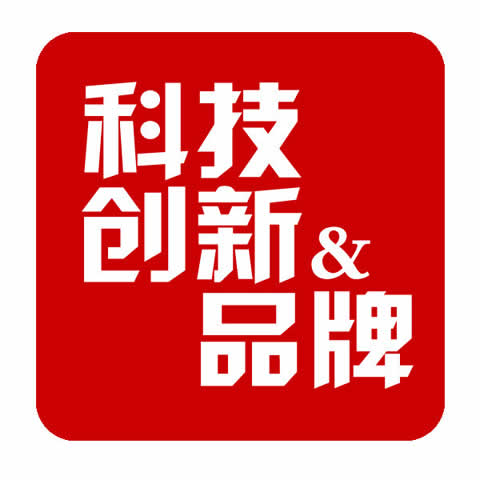