摘要:石油化工行业部分重要精密分析仪表外排尾气富含挥发性有机物(VOCs),属于无组织排放,对人身健康造成较大负面影响,且不能满足环保排放要求。文章通过对分析仪表当前可用VOCs处理技术、不同尾气组成、催化剂选材及载体的研究,开发一整套分析仪表尾气催化燃烧处理装置,并成功应用于石化装置,取得良好效果,达到国家排放标准,填补了国内在分析仪表尾气处理领域的技术空白。
关键词:分析仪表;VOCs;催化燃烧;催化剂;载体
1 引言
挥发性有机物(VOCs)是指常温下饱和蒸汽压大于70 Pa、常压下沸点在260℃以下的有机化合物,或在20℃条件下蒸汽压大于或者等于10 Pa具有相应挥发性的全部有机化合物【1】,在油田开采、炼化过程、造纸、汽车、电子等行业,以及家具装修、热交换系统、管道排放物等均会产生。为加强对VOCs无组织排放的控制和管理,国家已于2019年7月1日颁布实施《挥发性有机物无组织排放控制标准(GB37822-2019)》,标志着挥发性有机化合物(VOCs)的管控已成为现阶段我国大气环境治理领域中的重点和热点,其中石油化工行业属于重点管控行业。石油化工企业精密分析仪表有着广泛的应用,如何加强分析仪表VOCs尾气无害化处理,已成为刻不容缓的课题。
2 分析仪表VOCs治理现状分析
石油化工企业生产过程基本上采用全封闭的反应系统、全封闭的合成车间和全封闭放空和泄压系统,对富含VOCs的工艺尾气,设立专门的火炬气收集系统,用于回收利用或者焚烧净化等环境无害化处理,但是,在分析仪表等专用设备的尾气外排管控存在技术盲区。石油化工企业分析仪表常用的几类如质量分析仪表、色谱分析仪表、组分分析仪表等,运行过程通常需要利用工艺流程自身压差,以驱动分析仪表的复杂运转,换言之,分析仪表运行过程要求后续背压接近甚至低于大气压,与目前石化企业普遍采用微正压的火炬气收集系统相冲突。由于存在背压,分析仪表实际运行过程中易出现影响分析仪的测量精度,导致分析仪表故障率增加,以及增加分析仪表运营成本的问题。因此研究团队着手研究开发一套安装在分析仪表出口的性价比高、VOCs尾气处理效果显著的新装置。
3 VOCs处理技术研究及产品设计
通过对比浓度较高常用的直接燃烧法、吸附法、冷凝法、吸收法以及浓度较低常用的生物处理技术、膜分离技术、光催化法和催化燃烧法。相比于其他典型VOCs处理技术,催化燃烧法因具有起燃温度低、能耗低、催化效率高、使用范围广、操作安全等优点。结合分析仪表尾气的排放浓度,排放频率及排放组分等特点,分析得出催化燃烧技术匹配度较高,适用性更宜,可操作性更强,研究团队决定基于催化燃烧法处理技术,研发一套智能化在线分析仪表尾气VOCs净化处理装置。
3.1 技术原理
分析仪表VOCs有机尾气通过控制低温加热涂覆催化剂的载体,在催化剂的作用下,使有机性气体高温催化氧化分解成二氧化碳和水,从而无害化、无污染的排放到环境空气中。
催化燃烧法化学公式如下:
3.2 VOCs催化燃烧催化剂选择与制备
对于催化燃烧技术来说,最核心的是催化剂,其作用是降低反应的活化能,同时使反应物分子富集于催化剂表面,以提高反应速率,又称无焰燃烧。且应具有较高的氧化活性的特点,使反应在更低的温度下进行。常用的催化剂有非贵金属氧化物及其复合物、钙钛矿型催化剂、贵金属催化剂【2】。
3.2.1 非贵金属氧化物及其复合物
单一非贵金属氧化物催化剂是以存在 d 空轨道元素为主的过渡金属氧化物,如MnOx、CeO2、CoOx、NiO、ZrO2 等,这类过渡金属氧化物对CH4等烃类和CO的氧化都具有催化活性,但对苯类、环己酮、苯乙烯等催化活性不高,研究发现,金属氧化物的复合会产生金属离子间的取代从而在催化剂表面形成固溶体,提升催化剂低温还原性能。
3.2.2 钙钛矿型催化剂
钙钛矿是VOCs消除常用的催化剂之一,其通式为ABO3。含有一种或多种稀土元素的钙钛矿往往具有较好的VOCs消除催化活性和寿命。
3.2.3 贵金属催化剂
贵金属催化剂主要以Pt,Pb,Au等金属为主,这类催化剂通常附在载体上,通过总结发现,贵金属催化活性较非贵金属氧化物及其复合物、钙钛矿催化剂显著提升。
石化行业分析仪表尾气VOCs气体为苯系及烃类有机物,Pt更表现出了更强的催化活性,通过催化氧化苯、甲苯和正己烷及其混合物的实验发现在 180 ℃ 以下能将 VOCs 降解95%。纵向比较了不同类型催化剂对苯系,烷烃等有机物气体处理结果,本项目铂催化剂最为合适。
表1 非贵金属氧化物及其复合物催化作用
表2 钙钛矿型催化剂催化作用
表3 贵金属催化剂催化作用
3.2.4 催化剂制备
本课题研发的分析仪VOCs尾气处理装置采用的是浸渍法。浸渍法是将制备好的整体式催化剂载体置于含有活性组分的溶液中进行浸渍,按照设定的条件浸渍完成后,再通过干燥、焙烧、活化等步骤即可制成整体式催化剂载体,制备技术简单,可实施性强,Pt催化剂制备流程图如下:
3.3 催化剂载体研究
目前实际应用的催化燃烧催化剂大多为负载型催化剂,载体是催化剂的重要组成部分,其性能直接关系到催化剂的转化率、使用寿命和整个催化燃烧的装配要求,对整个催化燃烧系统的性能都有很大的影响,理想的催化剂载体应具备如下特点:(1)足够大的比表面积;(2)催化剂载体与活性物种强结合作用;(3)良好的机械强度;(4)足够的耐高温性,抗氧化作用;(5)较低的热膨胀系数和热容量;从催化燃烧研究现状及目前市场使用情况,载体材料主要有两种:不锈钢载体和蜂窝陶瓷载体材料。
3.3.1 不锈钢催化剂载体
不锈钢催化剂载体具备以下优势,(1)不锈钢载体的壁厚可以降到0.04mm左右,大大增加了其有效截面,从而降低阻力;(2)不锈钢可以订做成任意形状;(3)不锈钢载体具有良好的导热性能,可以快速传递热量,从而达到启动温度。研究团队开展对不锈钢载体结构的研究,设计了片状不锈钢网、嵌套式不锈钢蛇形盘管、不锈钢蛇形盘管内嵌蜂窝陶瓷载体等3种载体结构。
3.3.2 蜂窝陶瓷催化剂载体
蜂窝陶瓷是目前应用最广的催化剂载体材料,常见的蜂窝陶瓷催化剂载体【3】,如堇青石、莫来石、钛酸氯、碳化硅和氧化锆等。蜂窝陶瓷催化剂载体具备以下优势:(1)催化剂载体与涂层结合力较强,不易脱落,可实现贵金属催化剂活性物种高强度负载;(2)蜂窝陶瓷结构具有吸附性强且热膨胀性小等特点,利于制得低热膨胀的蜂窝载体,可使制品具有孔壁薄等特点,能使催化剂迅速达到活化温度;(3)蜂窝陶瓷载体还具有气体阻力小、机械强度高和抗热冲击性良好等优势;(4)热稳定性好、比表面积大、催化活性涂层薄,再加之成本较低,商业运用广阔。
经过对比不锈钢载体与蜂窝陶瓷载体,不锈钢具有重大缺陷,不锈钢载体与贵金属催化剂之间存在较大的热膨胀系数差别,使得贵金属与不锈钢金属结合力较差,往往需要进行酸洗、喷砂等表面处理形成大量新增孔再氧化处理,最后经过浸渍工艺在不锈钢网上形成一层薄涂层,工艺繁琐,即便经过一系列表面处理后,涂层易脱落,催化剂活性物种负载效果不理想。VOCs气体催化剂载体倾向于选择蜂窝陶瓷载体。
3.4 分析仪VOCs尾气处理装置产品设计
根据上述研究结论,完成最终产品设计:
本产品主体结构包括:加热系统,催化系统,气路系统,防爆系统。加热系统包括三部分,螺旋蛇形加热套管、温度控制器和传感器,蛇形加热套管实际加热面积大,纵向延伸,可使催化剂均匀受热,简单高效。温度控制器控制加热管温度,保证催化剂处于工作范围。催化系统以微米级颗粒陶瓷为载体,采用特殊工艺负载1-2nm贵金属催化剂,贵金属铆合在高比表面积载体上,用于低温催化燃烧苯系、烷烃等VOCs气体。颗粒陶瓷催化剂致密填充,与加热套管紧密接触。VOCs气体经进气口进入,通过催化主体结构,实现转换。防爆系统采用金属防爆网,符合国家安全标准,并取得防爆认证。本产品在240℃时即可实现浓度4000mg/m3苯,及二甲苯等含苯有机物98%以上转化,使用寿命2年。实现加热,催化燃烧一体化、小型化,可广泛运用于石化,电子,汽车等行业。结构图见图5,分析仪VOCs尾气处理装置实物见图6。
图1 片状不锈钢网载体剖面图
图2 片状不锈钢网载体左视图
图3 嵌套式不锈钢蛇形盘管载体
图4 不锈钢蛇形盘管内嵌蜂窝陶瓷载体
图5 分析仪VOCs尾气处理装置结构图
图6 分析仪VOCs尾气处理装置实物
6 结语
分析仪表尾气VOCs处理装置投用后,经实验证明,分析仪表处理后外排尾气VOCs指标满足《挥发性有机物无组织排放控制标准(GB37822-2019)》要求,解决了环境污染问题,控制了无组织排放要求,有利于分析仪表稳定运行,发挥了精密仪表在石油化工企业生产运行指导和质量保障的作用,填补了国内技术空白。此外,该技术在电子、汽车行业VOCs治理应用也有很大的推广价值。
参考文献
[1] GB37822-2019.挥发性有机物无组织排放控制标准.中国环境出版集团,2019
[2] 李鹏,童志权.“三苯系”VOCs催化燃烧催化剂的研究进展[J].工业催化.2006,14(8):1-6
[3] 谢云龙.堇青石陶瓷蜂窝涂载非贵金属符合催化剂的VOCs的催化性能研究[D].浙江工业大学.2006
责编/杨鑫
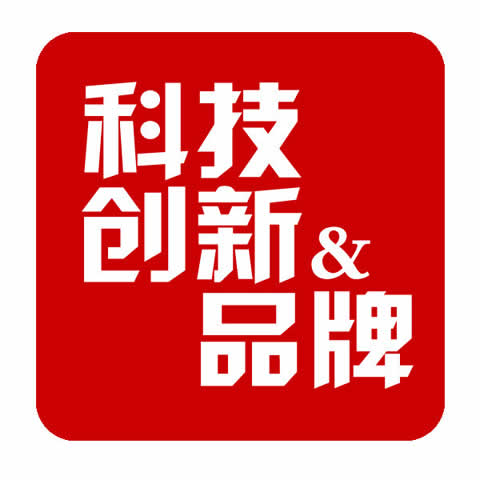