大飞机炭刹车盘制造技术实现突破性进展
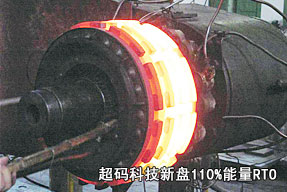
炭/炭复合材料自1958年问世以来,经历了五十多年的发展历程,已是一种成熟的技术,也是当今世界上发展最快,并最具应用潜力的热结构复合材料之一。由于炭/炭复合材料兼具摩擦特性好、使用寿命长、吸热能力高等无可比拟的优势,已成为飞机刹车盘的首选材料,并发展成炭/炭复合材料应用领域的最大独立市场,其年产量达到1200吨。主要由法国的Messier-Bugatti,美国的Hitco、Honeywell、Goodrich,英国的Dunlop五大公司垄断了国际市场。
我国民航引进装备炭刹车盘的飞机已达600余架,按平均2000次起落/套的使用寿命计算,炭刹车盘年更换约为3000套,按国外原厂目录价计算,市场年需求约7.5亿元人民币,全部依赖进口。
我国在1972年启动军用飞机炭刹车盘的探索研究,主要有西安航空制动科技有限公司、兰州炭素厂、上海炭素厂等单位参与。当时研制的第一代炭刹车盘材料为炭布叠层预制体、等温法CVI致密工艺制成的炭刹车盘材料,1984年开始进行整体结构炭盘大样的台架模拟试验。1987年,西安航空制动科技有限公司、兰州炭素厂研制的炭刹车盘材料被JH7飞机的第二配套方案确定采用,1991年2月通过中国航空机载设备总公司组织的技术评审。由兰州炭素厂研制的炭刹车盘于1990年7月在歼-7M型飞机上首次装机飞行试验获得成功,1998年由西安航空制动科技有限公司研制的炭刹车盘装在某重点型号飞机首飞成功,实现了我国军用飞机炭刹车盘零的突破。
20世纪90年代初启动大型民用飞机炭刹车盘材料研究工作的,有中南大学的湖南博云新材料有限公司、航天四十三所的西安超码科技有限公司、北京航空材料研究院的百慕高科技有限公司、西安航空制动科技有限公司、烟台鲁航炭材料科技有限公司等企业。研制的第二代炭刹车盘材料以针刺炭纤维准三向整体毡结构预制体,以等温法CVI致密的热解炭或以热梯度CVI与液相浸渍/炭化相结合的热解炭、树脂炭双元基体,制成了炭刹车盘材料。经过艰苦攻关,湖南博云新材料公司于2003年12月、西安超码科技有限公司于2004年5月分别取得波音757-200型飞机炭刹车盘的PMA生产许可证,百慕高科技有限公司于2005年8月取得MD-90型飞机炭刹车盘PMA生产许可证,西安超码科技有限公司于2009年3月率先取得A318/A319/A320型飞机炭刹车盘PMA生产许可证。
大飞机的刹车系统采用盘式结构,通常有动盘、静盘、压紧盘、承压盘等7~11片组套。动盘随机轮转动,其余炭盘与机轮轴连接,当刹车时,通过液压系统施加的压力将炭盘压紧,其间产生摩擦力矩,使飞机减速,同时炭刹车盘吸收的动能转换为热能。炭刹车盘的摩擦功能作为飞机刹车材料的结构、摩擦、吸热三大功能中最为关键的功能,用于飞机的滑行、着陆、停机和中止起飞等各种条件下的停机刹车、差动刹车、自动刹车、正常刹车、应急刹车、起落架收上时主轮的止转刹车等。
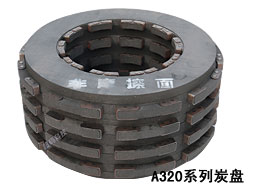
西安超码科技有限公司为了提高飞机炭刹车盘的单位能载、刹车特性和使用寿命,设计了新型铺层方式针刺炭纤维准三向结构预制体,提高了预制体的防分层和整体性能;发明了狭缝定向流“外热内冷”、“内热外冷”径向热梯度化学气相渗透致密工艺技术,获得了高摩擦特性的粗糙层热解炭;发展了一种热解炭、树脂炭优化组合的双元炭基体,解决了中止起飞刹车时摩擦系数严重衰减的问题;通过高温处理技术优化了摩擦特性,降低了磨损率,延长了使用寿命;研发的改性磷酸盐基涂层显著提高了抗氧化性能;设计了新型钢夹/铆钉配件,保障了炭刹车盘的安全使用;发明了原位炭补强的整体粘接修复炭刹车盘的维修方法,提高了炭刹车盘维修的整体可靠性。与A320系列飞机现用进口的炭刹车盘实测性能和刹车特性相比,本项目研制生产的五批次炭刹车盘的力学性能和轴向导热系数均有显著提高:经地面台架500余次动力矩试验对比,摩擦特性相当,中止起飞时的动摩擦系数提高了21%~42%,静摩擦系数提高了28%。7项飞行试验考核以及装机应用8个多月的实际磨损率测试结果表明,预计使用寿命可提高25%左右。
西安超码科技有限公司研制、生产的A318/A319/A320型飞机炭刹车盘与现用进口炭刹车盘具有一致的刹车性能及良好的系统兼容性,且无需更改飞行手册给定的起飞和着陆性能数据,即可保证飞机的正常使用。
该技术开发成果,在国内首次取得高能载、长使用寿命、高摩擦特性等重大关键技术的突破,使我国大型飞机炭刹车盘材料技术实现了跨越式发展,占据了大飞机刹车材料领域的制高点,达到了同类产品的国际先进水平。该成果不但打破了国外的技术垄断,实现了替代进口产品,降低了民航行业的运营成本,而且还为其他大型飞机炭刹车盘项目的开发应用奠定了技术基础,使我国步入生产大飞机炭刹车盘材料的国际先进行列,解决了大飞机行业发展中的热点、难点和关键问题之一,促进了大飞机制造行业的快速、协调发展。